WG Smart Drying Technology
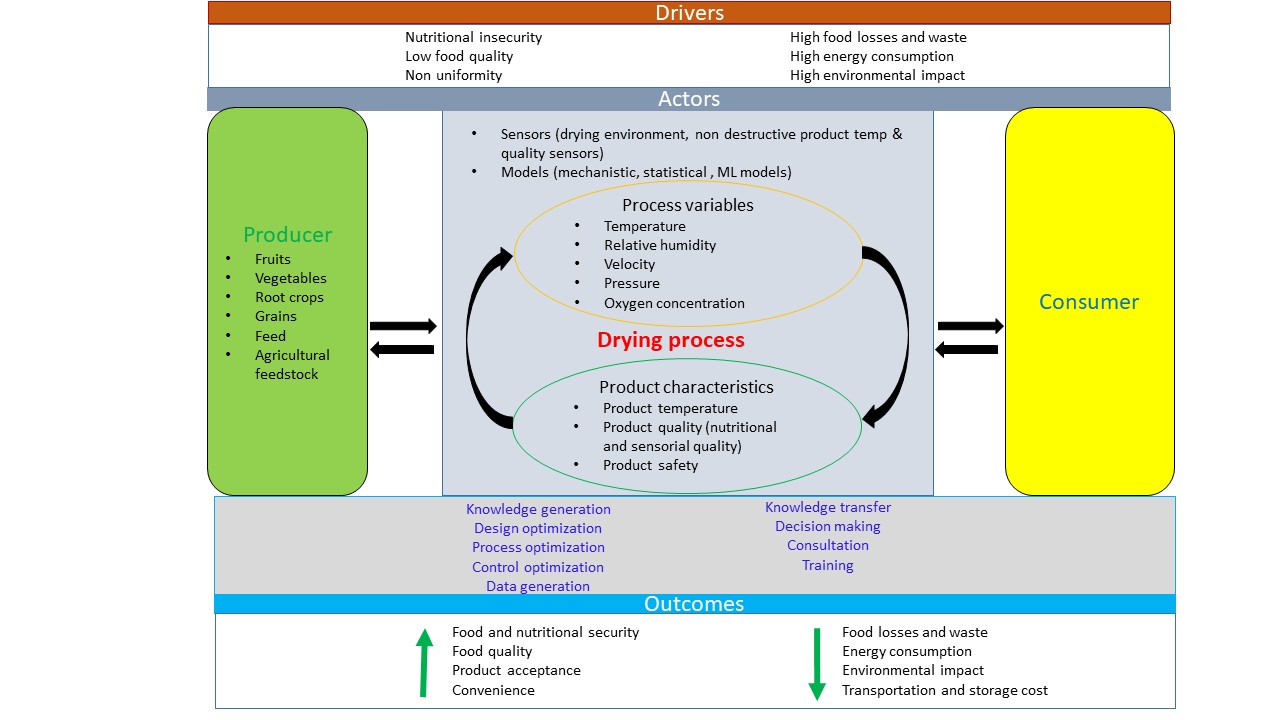
WG Smart Drying Technology conducts research innovative drying solutions to maximize product quality, safety, uniformity, and customer acceptance, while minimizing energy and resource consumption.
Research Focus Areas:
We utilise basic, applied, interdisciplinary research and co-creation approaches to develop novel intelligent drying systems using theoretical, experimental, computational and participatory design approaches with a key focus on:
Drying Quality and Efficiency:
Drying is a complex and energy intensive processing operation. Moreover, poorly designed drying systems have impart adverse changes in structure, texture, nutritional content, organoleptic properties and shelf life. At the WG Smart Drying Technology, we combine fundamental principles of heat and mass transfer, thermodynamics, mechanics and reaction engineering with numerical optimisation techniques to improve drying outcomes.
Smart Drying Systems:
Drying is a complex and energy intensive processing operation. Moreover, poorly designed drying systems have impart adverse changes in structure, texture, nutritional content, organoleptic properties and shelf life. At the WG Smart Drying Technology, we combine fundamental principles of heat and mass transfer, thermodynamics, mechanics and reaction engineering with numerical optimisation techniques to improve drying outcomes.
While we acknowledge the benefits accrued over years through the utilisation of conventional processing systems supported by traditional analytical techniques, we recognize their limitations for contemporary multi-objective real-time optimisation. At the WG Smart Drying Technology, we are implementing Quality-by-Design strategies to develop drying systems with real-time and non-destructive quality and process monitoring and control. We are integrating physical dryers with digital twins for adaptive process optimisation and control to improve energy efficiency, consistent product quality and predictable drying outcomes.

Sustainable Drying Solutions:
Amidst the ongoing triple planetary crisis, well-designed drying solutions are vital to achieving global sustainability goals. At the WG Smart Drying Technology, we are developing energy efficient drying systems that leverage bio-based materials and renewable energy sources. Technical, Environmental and Economic feasibility analyses are at the heart of our research and development workflows to innovate drying systems that are not only outstanding in serving their purpose but also minimises waste and emissions across the entire life cycle. We understand that the success of our systems is defined by their adoption by the target end users. We therefore factor in the inputs of the end user and economic metrics to enhance adoption and replication. We continually establish networks and collaborations with industrial partners, researchers and end users internationally to work on projects with shared objectives.
Novel Drying Technologies:
With the evolving tastes and preferences of food consumers and growing demand for highly nutritious conveniently available processed foods, we are actively investigating novel non-thermal and low heat drying techniques with particular benefits above conventional drying systems. At the WG Smart Drying Technology, we are investigating novel drying techniques including microwave, infrared and refractive window drying and combined with various novel pre-treatment methods and edible coatings.
Research Facilities:
Pilot-scale Dryers: Sensor-equipped Smart Dryer, Convective cabinet dryer, Deep-bed dryer, Mini wind tunnel.
Optical Sensor Systems: UV-Vis-NIR Hyperspectral Imaging Cameras, 3D Imaging Cameras, Thermal Imaging Cameras, RGB Cameras.
Analytical Equipment: Thermal gravimetric analyser (TGA), Time-Domain Nuclear Magnetic Resonance (TD-NMR), Near Infrared and Sorption Analysers, Reflectance Colorimeters and Particle Analysers.
Computational Resources: High-Performance Computing (HPC) Cluster, Computational Fluid Dynamics (CFD) software, Statistical and Design of Experiments software, Computer Aided Design (CAD) and 3D rendering software.
Controlled Environment Equipment: Mini wind tunnel, Climate chamber